Customized Hard Gold PCB Board FR4 Rigid Multilayer PCB Manufacturing
Basic Info
Model No. | PCB-A14 |
Transport package | Vacuum Packing |
Certification | UL,ISO9001&ISO14001,RoHS |
Application | Consumer electronics |
Minimum Space/Line | 0.075mm/3mil |
Production Capacity | 50,000 s.q.m/month |
HS Code | 853400900 |
Origin | Made in China |
Product Description
FR4 PCB Introduction
FR means “flame-retardant,” FR-4 (or FR4) is a NEMA grade designation for glass-reinforced epoxy laminate material, a composite material composed of woven fiberglass cloth with an epoxy resin binder that makes it an ideal substrate for electronic components on a printed circuit board.
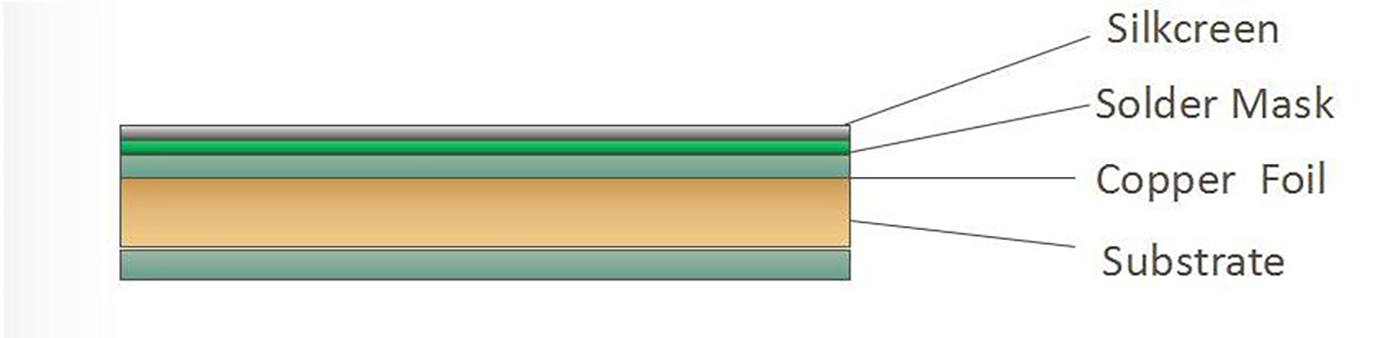
Pros and Cons of FR4 PCB
FR-4 material is so popular because of its many wondrous qualities that can benefit printed circuit boards. In addition to being affordable and easy to work with, it is an electrical insulator with very high dielectric strength. Plus, it's durable, moisture-resistant, temperature-resistant and lightweight.
FR-4 is a widely relevant material, popular mostly for its low cost and relative mechanical and electrical stability. While this material features extensive benefits and is available in a variety of thicknesses and sizes, it isn't the best choice for every application, especially high-frequency applications like RF and microwave designs.
Double sided PCBs Structure
Double sided PCBs are probably the most common type of PCBs. Unlike single layer PCBs, which have conductive layer on one side of the board, the Double Sided PCB comes with conductive copper layer on both sides of the board. Electronic circuits on one side of the board can be connected on the other side of the board with the help of holes (vias) drilled through the board. The ability to cross paths from top to bottom greatly increases the circuit designer's flexibility in circuits designing and lends itself to greatly increased circuit densities.
Multi-layer PCB Structure
Multilayer PCBs further increases the complexity and density of PCB designs by adding additional layers beyond the top and bottom layers seen in double sided boards. Multilayer PCBs are built by laminating the various layers. The inner-layers, normally double-sided circuit boards, are stacked together, with insulating layers in between and between the copper-foil for the outer-layers. Holes drilled through the board (vias) will make connections with the different layers of the board.
Where does the resin material come from in ABIS?
Most of them from Shengyi Technology Co., Ltd. (SYTECH), who has been the world's second largest CCL manufacturer in terms of sales volume, from 2013 to 2017. We established long-term relations of cooperation since 2006. The FR4 resin material (Model S1000-2, S1141, S1165, S1600) are mainly used for making single and double-sided printed circuit boards as well as multi-layer boards. Here comes details for your reference.
For FR-4: Sheng Yi, King Board, Nan Ya, Polycard, ITEQ, ISOLA
For CEM-1 & CEM 3: Sheng Yi, King Board
For High Frequency : Sheng Yi
For UV Cure: Tamura, Chang Xing ( * Available colour : Green) Solder for Single Side
For Liquid Photo: Tao Yang, Resist (Wet Film)
Chuan Yu ( * Available colours : White, Imaginable Solder Yellow, Purple, Red, Blue, Green, Black)
Technical & Capability
ABIS experienced in making special materials for rigid PCB, such as: CEM-1/CEM-3, PI, High Tg, Rogers, PTEF, Alu/Cu Base, etc. Below is a brief overview FYI.
Item | Production Capacity |
Layer Counts | 1-20 layers |
Material | FR-4, CEM-1/CEM-3, PI, High Tg, Rogers, PTEF, Alu/Cu Base, etc |
Board thickness | 0.10mm-8.00mm |
Maximum Size | 600mmX1200mm |
Board Outline Tolerance | +0.10mm |
Thickness Tolerance(t≥0.8mm) | ±8% |
Thickness Tolerance(t<0.8mm) | ±10% |
Insulation Layer Thickness | 0.075mm--5.00mm |
Minimum Line | 0.075mm |
Minimum Space | 0.075mm |
Out Layer Copper Thickness | 18um--350um |
Inner Layer Copper Thickness | 17um--175um |
Drilling Hole(Mechanical) | 0.15mm--6.35mm |
Finish Hole(Mechanical) | 0.10mm-6.30mm |
Diameter Tolerance(Mechanical) | 0.05mm |
Registration(Mechanical) | 0.075mm |
Aspect Ratio | 16:1 |
Solder Mask Type | LPI |
SMT Mini.Solder Mask Width | 0.075mm |
Mini. Solder Mask Clearance | 0.05mm |
Plug Hole Diameter | 0.25mm--0.60mm |
Impedance control Tolerance | ±10% |
Surface finish/treatment | HASL, ENIG, Chem, Tin, Flash Gold, OSP, Gold Finger |
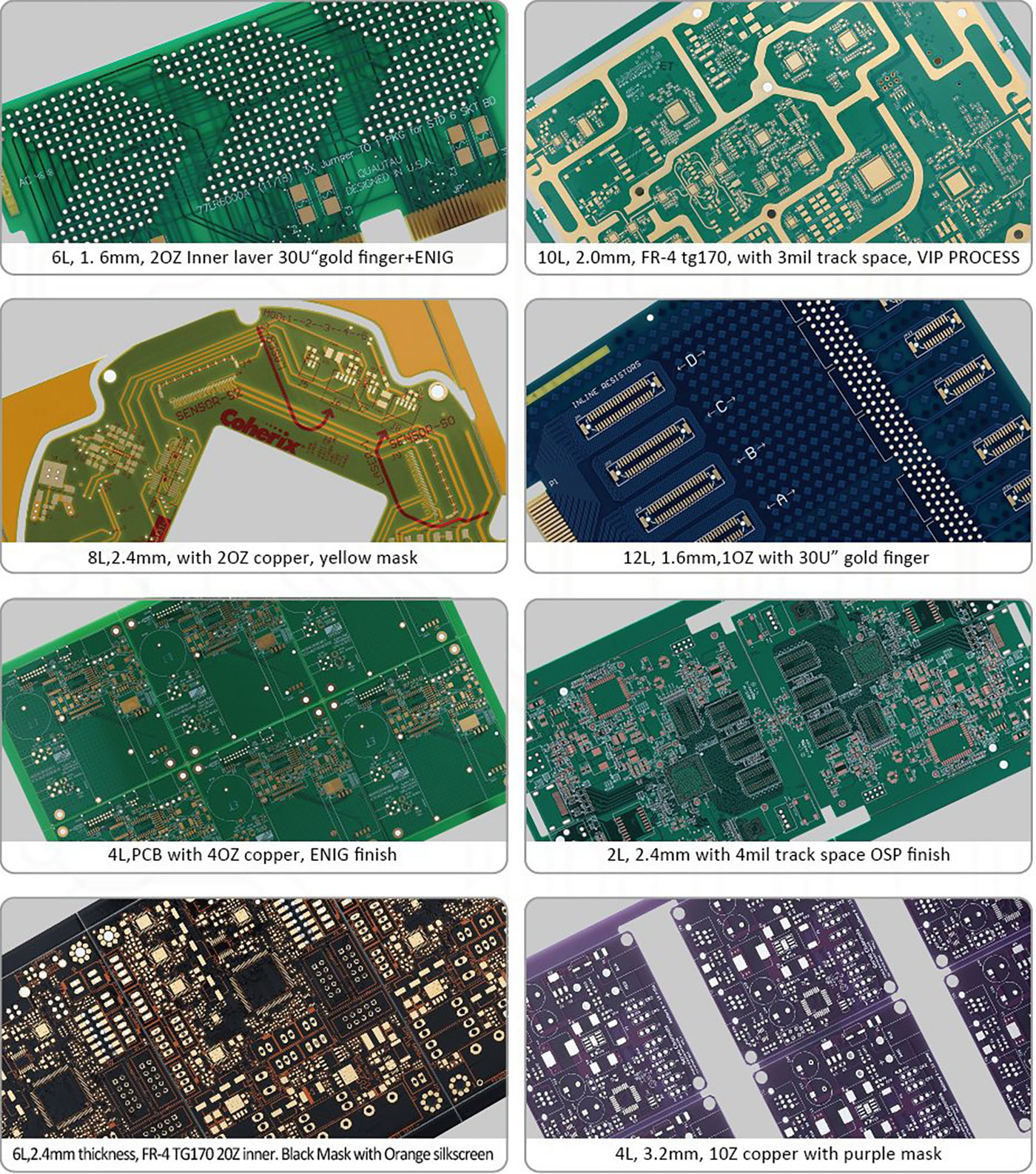
PCB Production Process
The process starts with designing Layout of the PCB using any PCB designing software / CAD Tool (Proteus, Eagle, Or CAD).
All rest of the steps are of Manufacturing Process of a Rigid Printed Circuit Board is same as Single Sided PCB or Double Sided PCB or Multi-layer PCB.
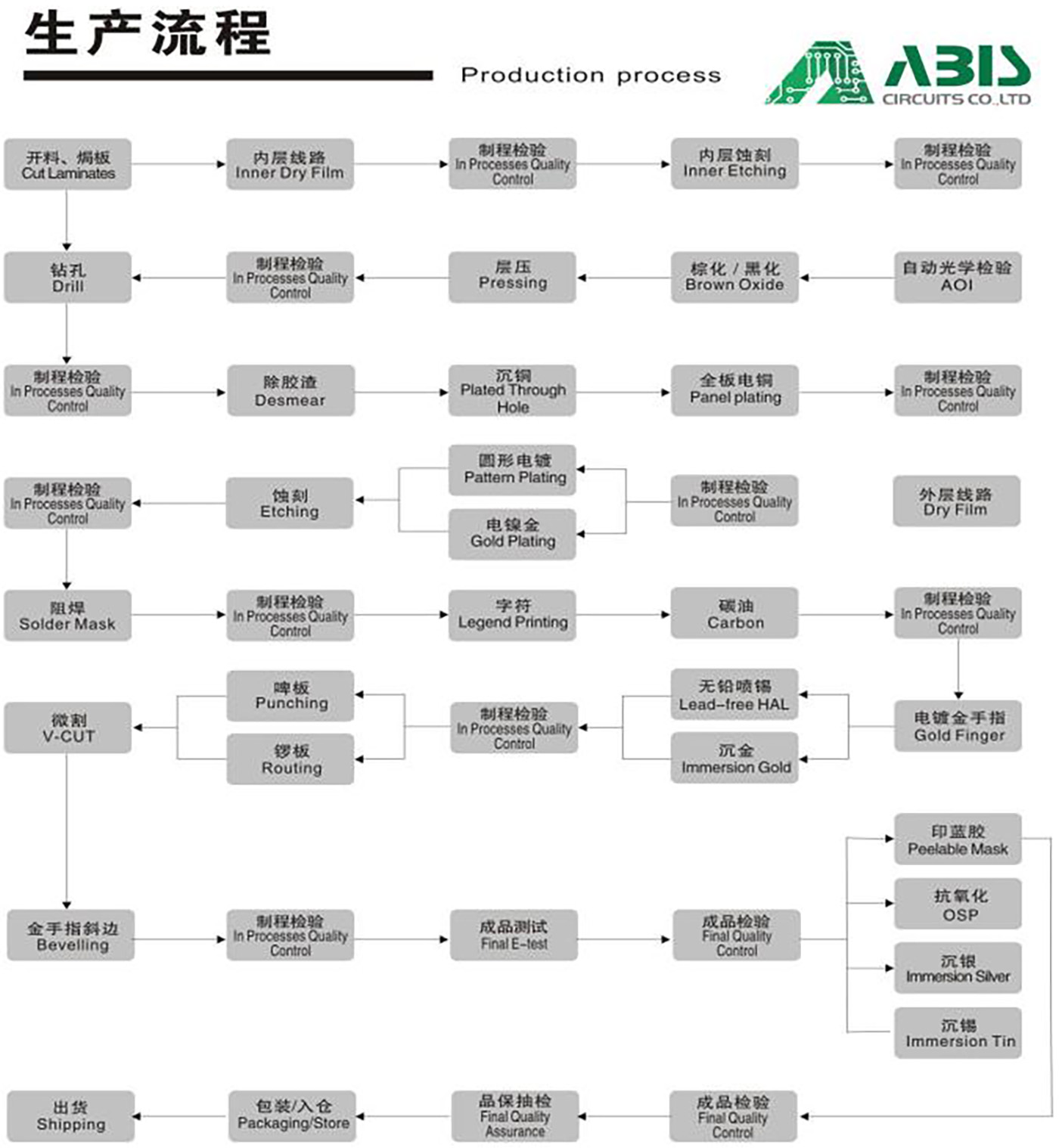
Q/T Lead Time
Category | Quickest Lead Time | Normal Lead Time |
Double-sided | 24hrs | 120hrs |
4 Layers | 48hrs | 172hrs |
6 Layers | 72hrs | 192hrs |
8 Layers | 96hrs | 212hrs |
10 Layers | 120hrs | 268hrs |
12 Layers | 120hrs | 280hrs |
14 Layers | 144hrs | 292hrs |
16-20 Layers | Depends on the specific requirements | |
Above 20 Layers | Depends on the specific requirements |
ABIS' move to control FR4 PCBS
Hole Preparation
Removing debris carefully & adjusting drill machine parameters: before plating through with copper, ABIS pays high attention to all holes on an FR4 PCB treated to remove debris, surface irregularities, and epoxy smear, the clean holes ensure the plating successfully adheres to the hole walls. also, early in the process, drill machine parameters are adjusted accurately.
Surface Preparation
Deburring carefully: our experienced tech workers will be aware ahead of time that the only way to avoid a bad outcome is to anticipate the need for special handling and to take the appropriate steps to be sure that the process is done carefully and correctly.
Thermal Expansion Rates
Accustomed to dealing with the various materials, ABIS will be able to analyze the combination to be sure that it is appropriate. then keeping the long-term reliability of the CTE (coefficient of thermal expansion), with the lower CTE, the less likely the plated through holes are to fail from repeated flexing of the copper which forms the internal layer interconnections.
Scaling
ABIS control the circuitry is scaled-up by known percentages in anticipation of this loss so that the layers will return to their as-designed dimensions after the lamination cycle is complete. also, using the laminate manufacturer’s baseline scaling recommendations in combination with in-house statistical process control data, to dial-in scale factors that will be consistent over time within that particular manufacturing environment.
Machining
When the time comes to build your PCB, ABIS be sure that you choose has the right equipment and experience to produce it correctly on the first try.
Quality Control
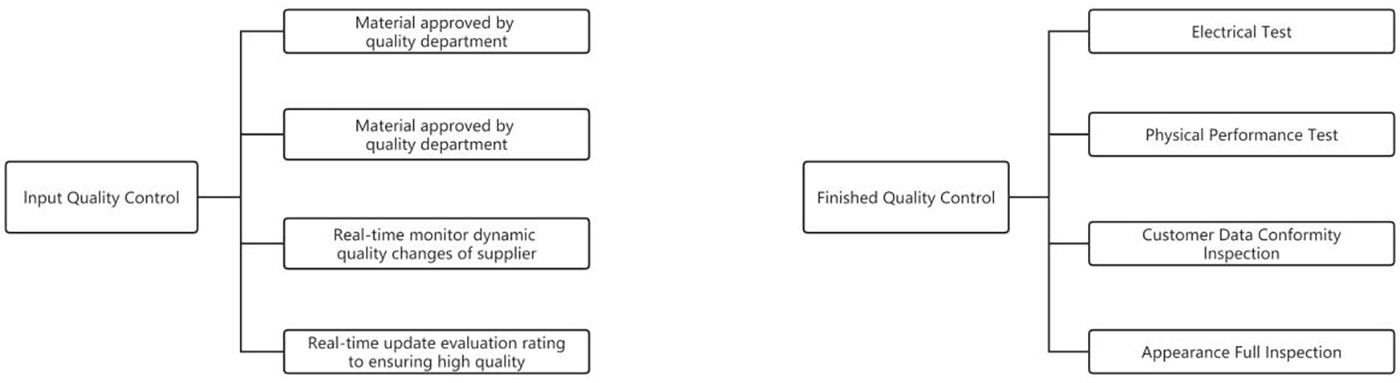
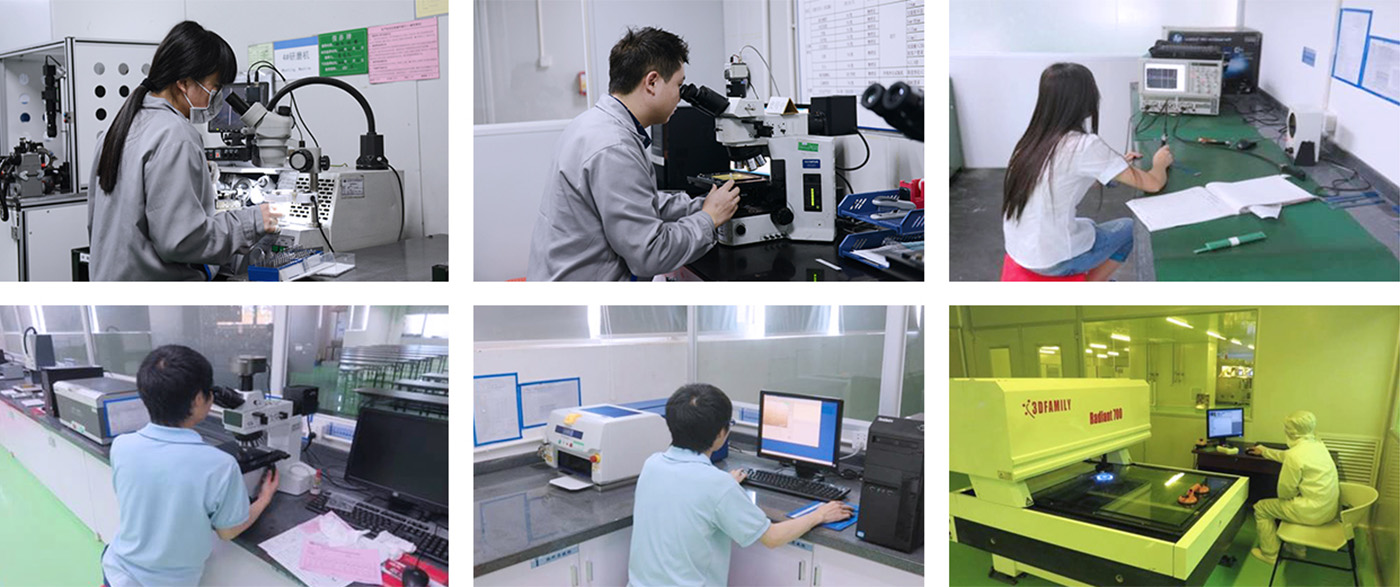
BIS solves the aluminum PCB problem?
Raw materials are strictly controlled: The pass rate of incoming material above 99.9%. The number of mass rejection rates is below 0.01%.
Copper Etching Controlled: the copper foil used in Aluminum PCBs is comparatively thicker. If the copper foil is over 3oz however, the etching requires width compensation. With the high precision equipment imported from Germany, the min width/space we can control reaches 0.01mm. The trace width compensation will be designed accurately to avoid the trace width out of tolerance after etching.
High Quality Solder Mask Printing: As we all know, there is a difficulty in solder mask printing of aluminum PCB due to copper thick. This is because if the trace copper is too thick, then the image etched will have a large difference between trace surface and base board and solder mask printing will be difficult. We insist on the highest standards of solder mask oil in the whole process, from the one to the two-time solder mask printing.
Mechanical Manufacturing: To avoid reducing electrical strength caused by the mechanical manufacturing process, involves mechanical drilling, molding and v-scoring etc. Therefore, for low-volume manufacturing of products, we prioritize using the electric milling and professional milling cutter. Also, we pay high attention to adjusting the drilling parameters and preventing burr from generating.
Certificate
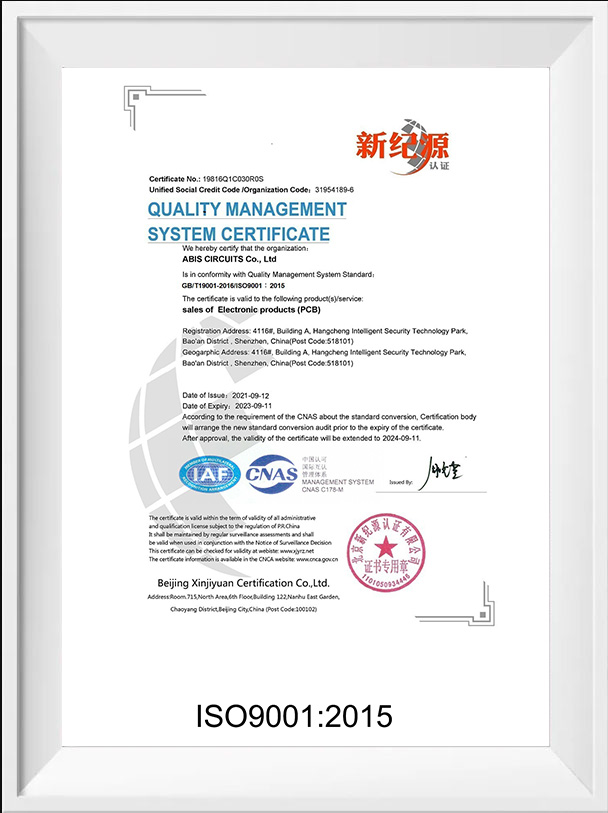
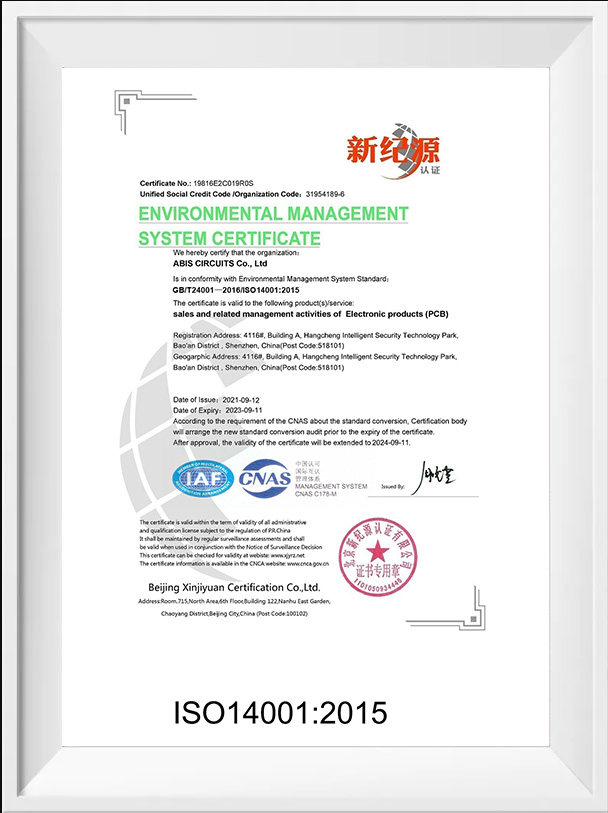
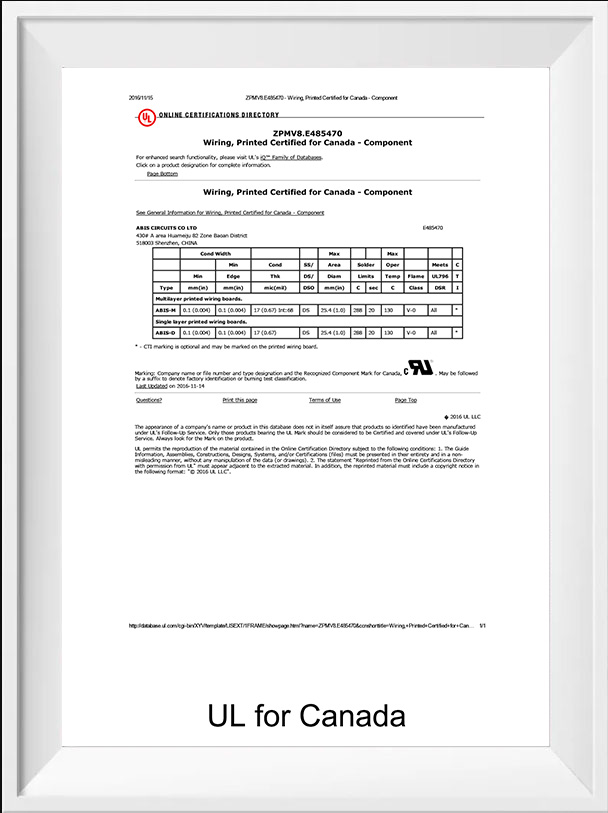
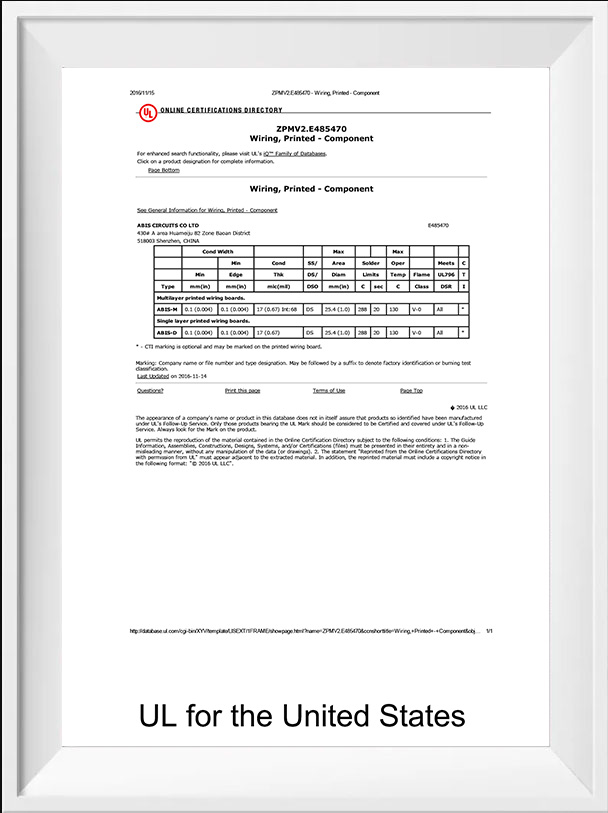
FAQ
Checked within 12 hours. Once Engineer's question and working file checked, we'll start the production.
ISO9001, ISO14001,UL USA& USA Canada,IFA16949, SGS, RoHS report.
Our Quality Assuring Procedures as below:
a),Visual Inspection
b),Flying probe, fixture tool
c), Impedance control
d), Solder-ability detection
e), Digital metallo graghic microscope
f),AOI (Automated Optical Inspection)
No, we can't accept picture files, if you no not have Gerber file, can you send us sample to copy it.
PCB&PCBA Copy Process:
On time delivery rate is more than 95%
a),24 hours fast turn for double side prototype PCB
b),48hours for 4-8 layers prototype PCB
c),1 hour for quotation
d),2 hours for engineer question/Complaint feedback
e),7-24 hours for technical support/order service/manufacturing operations
ABIS has no MOQ requirements for either PCB or PCBA.
We participate in exhibitions every year, the most recent being the Expo Electronica&ElectronTechExpo in Russia dated April 2023. Look forward to your visit.
ABlS performs 100% visual and AOl inspection as well as performing electrical testing, high voltage testing, impedance control testing, micro-sectioning, thermal shock testing, solder testing, reliability testing, insulating resistance testing, ionic cleanliness testing and PCBA Functional testing.
a),1 Hour quotation
b),2 hours of complaint feedback
c),7*24 hour technical support
d),7*24 order service
e),7*24 hour delivery
f),7*24 production run
Production capacity of hot-sale products | |
Double Side/Multilayer PCB Workshop | Aluminum PCB Workshop |
Technical Capability | Technical Capability |
Raw materials: CEM-1, CEM-3, FR-4(High TG), Rogers, TELFON | Raw materials: Aluminum base, Copper base |
Layer: 1 layer to 20 Layers | Layer: 1 layer and 2 Layers |
Min.line width/space: 3mil/3mil(0.075mm/0.075mm) | Min.line width/space: 4mil/4mil(0.1mm/0.1mm) |
Min.Hole size: 0.1mm(dirilling hole) | Min. Hole size: 12mil(0.3mm) |
Max. Board size: 1200mm* 600mm | Max.Board size: 1200mm* 560mm(47in* 22in) |
Finished board thickness: 0.2mm- 6.0mm | Finished board thickness: 0.3~ 5mm |
Copper foil thickness: 18um~280um(0.5oz~8oz) | Copper foil thickness: 35um~210um(1oz~6oz) |
NPTH Hole Tolerance: +/-0.075mm, PTH hole Tolerance: +/-0.05mm | Hole position tolerance: +/-0.05mm |
Outline Tolerance: +/-0.13mm | Routing outline tolerance: +/ 0.15mm; punching outline tolerance:+/ 0.1mm |
Surface finished: Lead-free HASL, immersion gold(ENIG), immersion silver, OSP, gold plating, gold finger, Carbon INK. | Surface finished: Lead free HASL, immersion gold(ENIG), immersion silver, OSP etc |
Impedance control tolerance: +/-10% | Remain thickness tolerance: +/-0.1mm |
Production capability: 50,000 s.q.m/month | MC PCB Production capability: 10,000 s.q.m/month |