6 layers Hard Gold PCB Board with 3.2mm board thickness and Counter Sink Hole
Basic Info
Model No. | PCB-A37 |
Transport package | Vacuum Packing |
Certification | UL,ISO9001&ISO14001,RoHS |
Application | Consumer electronics |
Minimum Space/Line | 0.075mm/3mil |
Production Capacity | 50,000 s.q.m/month |
HS Code | 853400900 |
Origin | Made in China |
Product Description
HDI PCB Introduction
HDI PCB is defined as a printed circuit board with a higher wiring density per unit area than a conventional PCB. They have much finer lines and spaces, smaller vias and capture pads, and higher connection pad density than employed in conventional PCB technology. HDI PCBs are made through microvias, buried vias and sequential lamination with insulation materials and conductor wiring for higher density of routing.
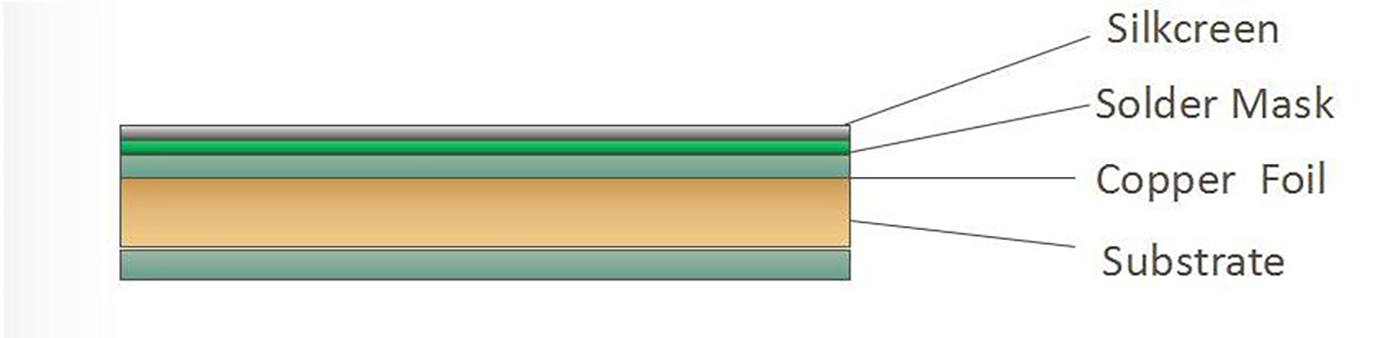
Applications
HDI PCB is used to reduce size and weight, as well as to enhance electrical performance of the device. HDI PCB is the best alternative to high layer-count and expensive standard laminate or sequentially laminated boards. HDI incorporate blind and buried vias that help to save PCB real estate by allowing features and lines to be designed above or below them without making a connection. Many of today's fine pitch BGA and flip-chip component footprints do not allow for running traces between the BGA pads. Blind and buried vias will only connect layers requiring connections in that area.
Technical & Capability
ITEM | CAPABILITY | ITEM | CAPABILITY |
Layers | 1-20L | Thicker Copper | 1-6OZ |
Products Type | HF(High-frequency) &(Radio Frequency)board, Imedance controlled board, HDIboard, BGA & Fine Pitch board | Solder Mask | Nanya & Taiyo; LRI & Matt Red. green,yellow, white, blue, black |
Base material | FR4(Shengyi China,ITEQ, KB A+,HZ),HITG,FrO6,Rogers,Taconic,Argon,Nalco lsola and so on | Finished Surface | Conventional HASL,Lead-free HASL,FlashGold,ENIG (lmmersion Gold) OSP (Entek),lmmersion TiN, lmmersion Silver,Hard Gold |
Selective Surface treatment | ENIG(immersion Gold) + OSP ,ENIG(immersion Gold) + Gold Finger, Flash Gold Finger, immersionSlive + Gold Finger, Immersion Tin + Gold Finger | ||
Technical Specification | Minimum line width/gap: 3.5/4mil (laser dril) Minimum hole size: 0.15 mm(mechanical drill/4 mill laser drill) Minimum Annular Ring: 4mil Max Copper thickness: 6Oz Max Production size: 600x1200mm Board Thickness: D/S: 0.2-70mm,Mulltilayers: 0.40-7.Omm Min Solder Mask Bridge: ≥0.08mm Aspect ratio: 15:1 Plugging vias capability: 0.2-0.8mm |
||
Tolerance | Plated holes Tolerance : ±0.08mm(min±0.05) Non-plated hole tolerance: ±O.05min(min+O/-005mm or +0.05/Omm) Outline Tolerance: ±0.15min(min±0.10mm) Functional test: lnsulating resistance: 50 ohms (normality) Peel off strength: 14N/mm Thermal Stress test: 265C.20 seconds Solder mask hardness: 6H E-test voltage: 50ov±15/-0V 3os Warp and Twist: 0.7%( semiconductor test board 0.3%) |
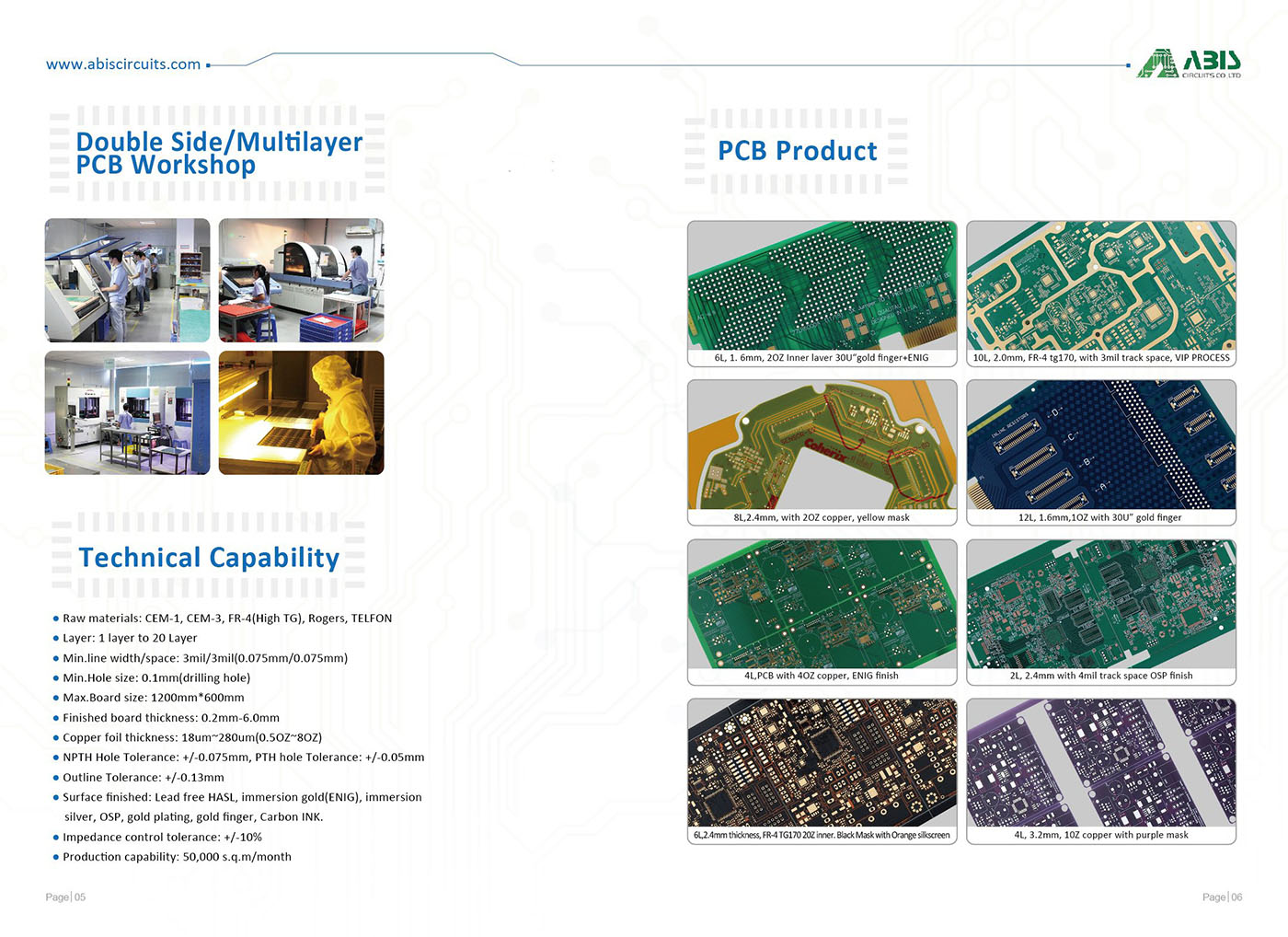
Features-Our Products Advantage
Morethan 15 years experience manufacturer in PCB service field
Big scale of producing makes sure that your purchase cost is lower.
Advanced production line guarantees stable quality and long life span
100% test for all customized PCB products
One-stop Service ,we can help to purchase the components
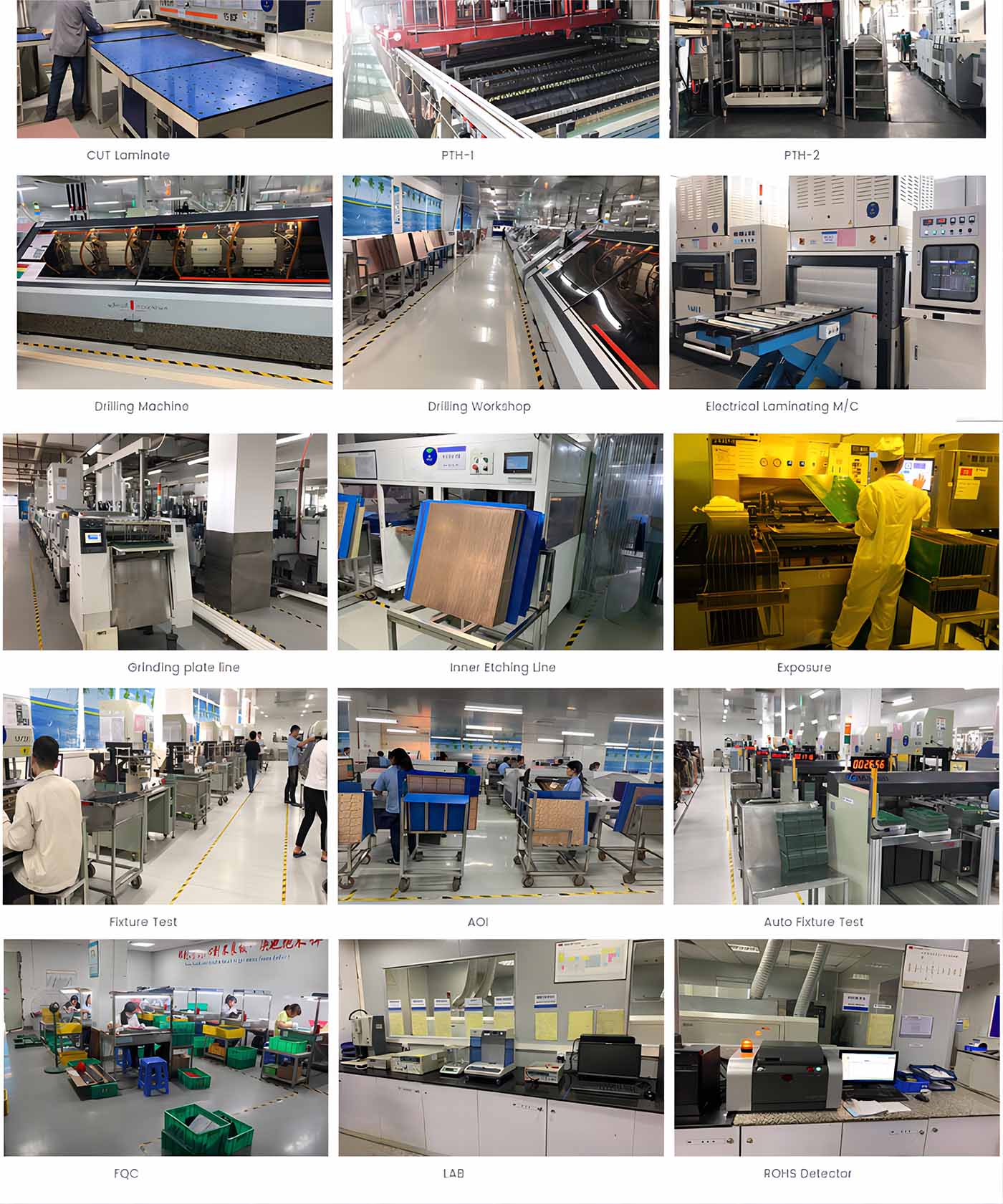
Q/T Lead Time
Category | Quickest Lead Time | Normal Lead Time |
Double-sided | 24hrs | 120hrs |
4 Layers | 48hrs | 172hrs |
6 Layers | 72hrs | 192hrs |
8 Layers | 96hrs | 212hrs |
10 Layers | 120hrs | 268hrs |
12 Layers | 120hrs | 280hrs |
14 Layers | 144hrs | 292hrs |
16-20 Layers | Depends on the specific requirements | |
Above 20 Layers | Depends on the specific requirements |
ABIS' move to control FR4 PCBS
Hole Preparation
Removing debris carefully & adjusting drill machine parameters: before plating through with copper, ABIS pays high attention to all holes on an FR4 PCB treated to remove debris, surface irregularities, and epoxy smear, the clean holes ensure the plating successfully adheres to the hole walls. also, early in the process, drill machine parameters are adjusted accurately.
Surface Preparation
Deburring carefully: our experienced tech workers will be aware ahead of time that the only way to avoid a bad outcome is to anticipate the need for special handling and to take the appropriate steps to be sure that the process is done carefully and correctly.
Thermal Expansion Rates
Accustomed to dealing with the various materials, ABIS will be able to analyze the combination to be sure that it is appropriate. then keeping the long-term reliability of the CTE (coefficient of thermal expansion), with the lower CTE, the less likely the plated through holes are to fail from repeated flexing of the copper which forms the internal layer interconnections.
Scaling
ABIS control the circuitry is scaled-up by known percentages in anticipation of this loss so that the layers will return to their as-designed dimensions after the lamination cycle is complete. also, using the laminate manufacturer’s baseline scaling recommendations in combination with in-house statistical process control data, to dial-in scale factors that will be consistent over time within that particular manufacturing environment.
Machining
When the time comes to build your PCB, ABIS be sure that you choose has the right equipment and experience to produce it
ABIS Quality Mission
The pass rate of incoming material above 99.9%, the number of mass rejection rates below 0.01%.
ABIS certified facilities control all key processes to eliminate all potential issues before producing.
ABIS utilizes advanced software to perform extensive DFM analysis on incoming data, and uses advanced quality control systems throughout the manufacturing process.
ABIS performs 100% visual and AOI inspection as well as performing electrical testing, high voltage testing, impedance control testing, micro-sectioning, thermal shock testing, solder testing, reliability testing, insulating resistance testing and ionic cleanliness testing.
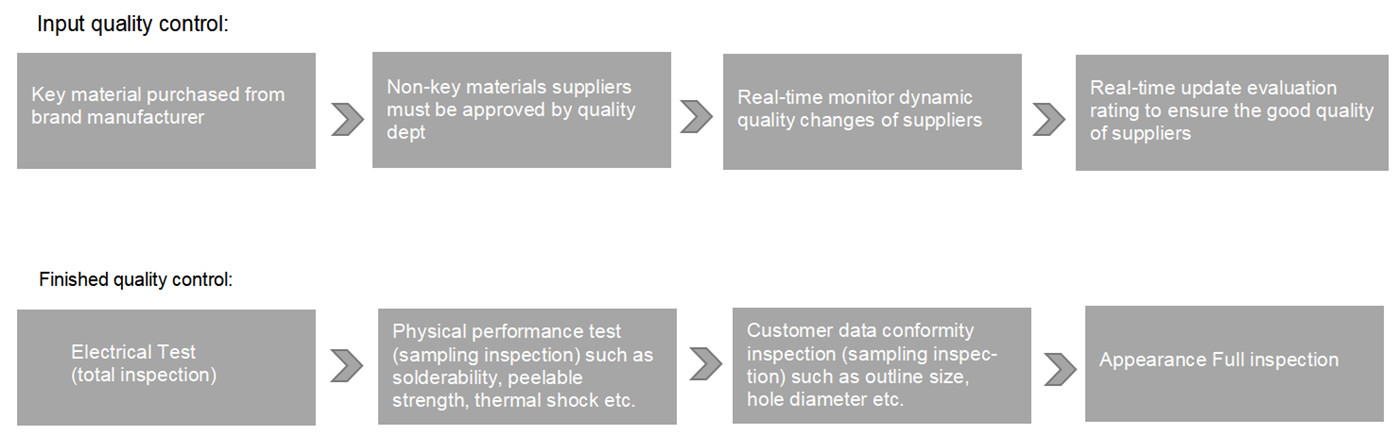
Certificate
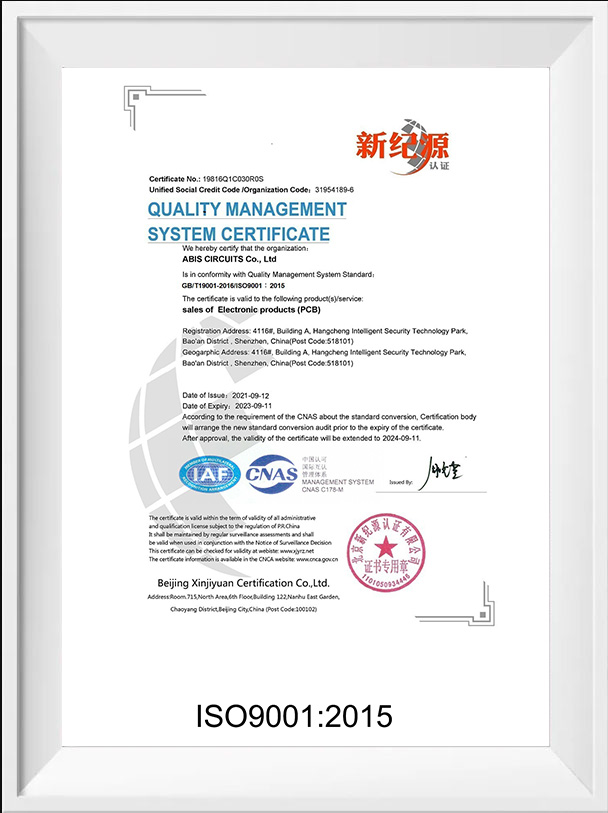
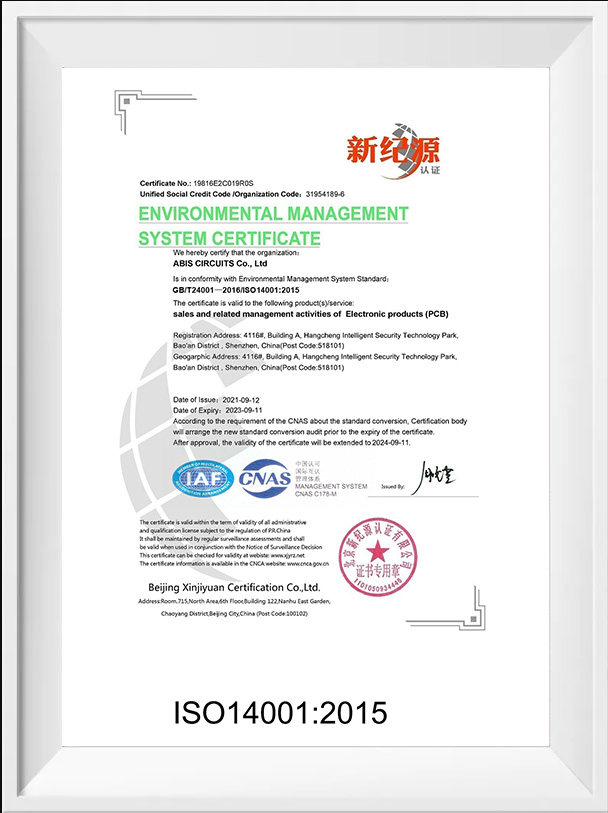
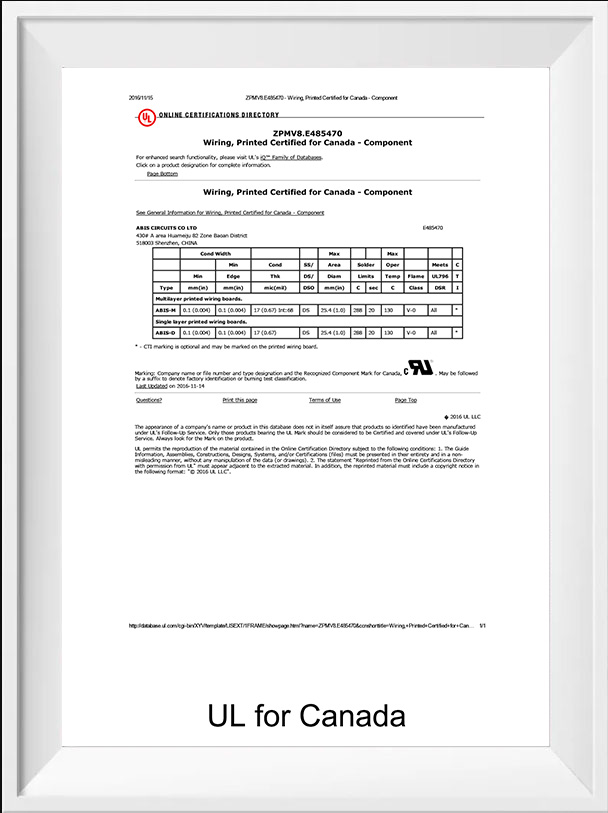
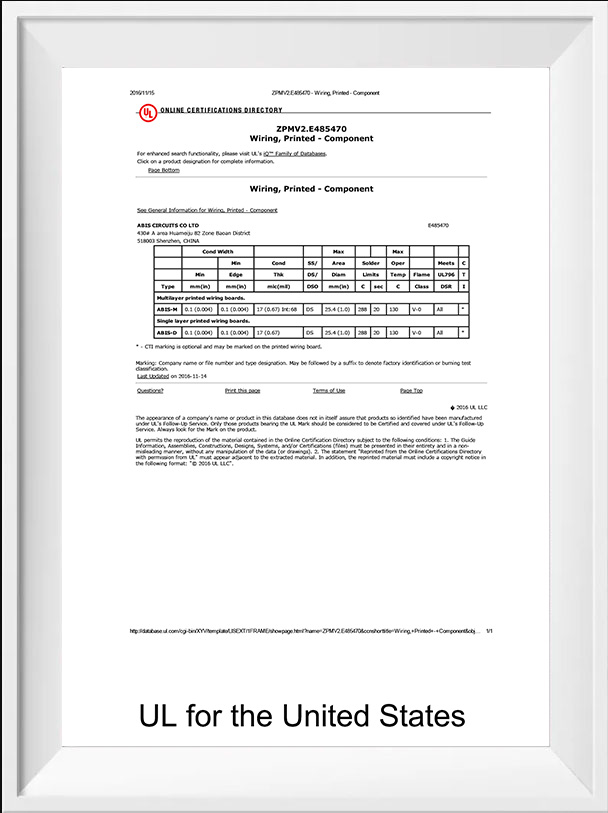
FAQ
Most of them from Shengyi Technology Co., Ltd. (SYTECH), who has been the world's second largest CCL manufacturer in terms of sales volume, from 2013 to 2017. We established long-term relations of cooperation since 2006. The FR4 resin material (Model S1000-2, S1141, S1165, S1600) are mainly used for making single and double-sided printed circuit boards as well as multi-layer boards. Here comes details for your reference.
For FR-4: Sheng Yi, King Board, Nan Ya, Polycard, ITEQ, ISOLA
For CEM-1 & CEM 3: Sheng Yi, King Board
For High Frequency : Sheng Yi
For UV Cure: Tamura, Chang Xing ( * Available colour : Green) Solder for Single Side
For Liquid Photo: Tao Yang, Resist (Wet Film)
Chuan Yu ( * Available colors : White, Imaginable Solder Yellow, Purple, Red, Blue, Green, Black)
),1 Hour quotation
b),2 hours of complaint feedback
c),7*24 hour technical support
d),7*24 order service
e),7*24 hour delivery
f),7*24 production run
No, we can't accept picture files, if you no not have Gerber file, can you send us sample to copy it.
PCB&PCBA Copy Process:
Our Quality Assuring Procedures as below:
a),Visual Inspection
b),Flying probe, fixture tool
c), Impedance control
d), Solder-ability detection
e), Digital metallo graghic microscope
f),AOI (Automated Optical Inspection)
On time delivery rate is more than 95%
a),24 hours fast turn for double side prototype PCB
b),48hours for 4-8 layers prototype PCB
c),1 hour for quotation
d),2 hours for engineer question/Complaint feedback
e),7-24 hours for technical support/order service/manufacturing operations
ABIS has no MOQ requirements for either PCB or PCBA.
ABlS performs 100% visual and AOl inspection as well as performing electrical testing, high voltage testing, impedance control testing, micro-sectioning, thermal shock testing, solder testing, reliability testing, insulating resistance testing, ionic cleanliness testing and PCBA Functional testing.
ABIS's Main Industries: Industrial Control, Telecommunication, Automotive Products and Medical. ABIS's Main Market: 90% International Market(40%-50% for USA, 35% for Europe, 5% for Russia and 5%-10% for East Asia) and 10% Domestic Market.
Production capacity of hot-sale products | |
Double Side/Multilayer PCB Workshop | Aluminum PCB Workshop |
Technical Capability | Technical Capability |
Raw materials: CEM-1, CEM-3, FR-4(High TG), Rogers, TELFON | Raw materials: Aluminum base, Copper base |
Layer: 1 layer to 20 Layers | Layer: 1 layer and 2 Layers |
Min.line width/space: 3mil/3mil(0.075mm/0.075mm) | Min.line width/space: 4mil/4mil(0.1mm/0.1mm) |
Min.Hole size: 0.1mm(dirilling hole) | Min. Hole size: 12mil(0.3mm) |
Max. Board size: 1200mm* 600mm | Max.Board size: 1200mm* 560mm(47in* 22in) |
Finished board thickness: 0.2mm- 6.0mm | Finished board thickness: 0.3~ 5mm |
Copper foil thickness: 18um~280um(0.5oz~8oz) | Copper foil thickness: 35um~210um(1oz~6oz) |
NPTH Hole Tolerance: +/-0.075mm, PTH hole Tolerance: +/-0.05mm | Hole position tolerance: +/-0.05mm |
Outline Tolerance: +/-0.13mm | Routing outline tolerance: +/ 0.15mm; punching outline tolerance:+/ 0.1mm |
Surface finished: Lead-free HASL, immersion gold(ENIG), immersion silver, OSP, gold plating, gold finger, Carbon INK. | Surface finished: Lead free HASL, immersion gold(ENIG), immersion silver, OSP etc |
Impedance control tolerance: +/-10% | Remain thickness tolerance: +/-0.1mm |
Production capability: 50,000 s.q.m/month | MC PCB Production capability: 10,000 s.q.m/month |